QR koodi
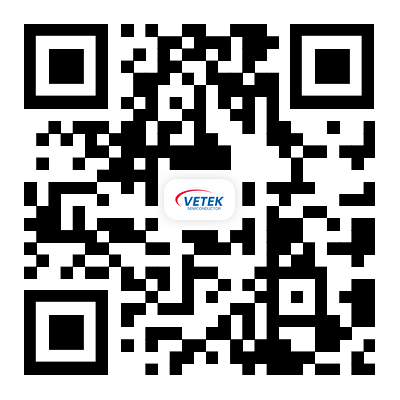
Meistä
Tuotteet
Ota meihin yhteyttä
Puhelin
Faksi
+86-579-87223657
Sähköposti
Osoite
Wangda Road, Ziyang Street, Wuyi County, Jinhua City, Zhejiangin maakunta, Kiina
Kunkin puolijohdetuotteen valmistus vaatii satoja prosesseja, ja koko valmistusprosessi on jaettu kahdeksaan vaiheeseen:Kiekkojen prosessointi - hapettuminen - fotolitografia - etsaus - ohutkalvojen laskeuma - toisiinsa - testaus - pakkaus.
Vaihe 5: Ohut kalvon laskeutuminen
Mikrolaitteiden luomiseksi sirun sisälle, meidän on jatkuvasti talletettava ohutkalvojen kerroksia ja poistettava ylimääräiset osat etsaamalla ja myös lisättävä joitain materiaaleja eri laitteiden erottamiseen. Jokainen transistori tai muistisolu on rakennettu askel askeleelta yllä olevan prosessin läpi. "Ohut elokuva", josta puhumme täällä, viittaa "kalvoon", jonka paksuus on alle 1 mikron (μm, miljoonasosa metristä), jota ei voida valmistaa tavallisilla mekaanisilla prosessointimenetelmillä. Kalvon vaadittavat molekyyli- tai atomiyksiköt, jotka sisältävät kalvon, asettamisprosessi on "laskeuma".
Monikerroksisen puolijohdirakenteen muodostamiseksi meidän on ensin valmistettava laitepino, ts. Vaihtoehtoisesti pino useita kerroksia ohuita metallikalvoja (johtavia) kalvoja ja dielektrisiä (eristäviä) kalvoja kiekkojen pinnalla ja poista sitten ylimääräiset osat toistuvien etsausprosessien avulla kolmiulotteisen rakenteen muodostamiseksi. Tekniikat, joita voidaan käyttää laskeutumisprosesseihin, sisältävät kemiallisen höyryn laskeutumisen (CVD), atomikerroksen laskeutumisen (ALD) ja fysikaalisen höyryn laskeutumisen (PVD), ja näitä tekniikoita käyttävät menetelmät voidaan jakaa kuivaan ja märään laskeutumiseen.
Kemiallinen höyryn laskeuma (CVD)
Kemiallisessa höyryn laskeutumisessa prekursorikaasut reagoivat reaktiokammiossa muodostaen ohutkalvon, joka on kiinnitetty kiekon pintaan ja sivutuotteet, jotka pumpataan kammiosta. Plasmaparannettu kemiallinen höyryn laskeuma käyttää plasmaa reagenssikaasujen tuottamiseen. Tämä menetelmä vähentää reaktiolämpötilaa, mikä tekee siitä ihanteellisen lämpötilaherkälle rakenteelle. Plasman käyttäminen voi myös vähentää laskeutumisten lukumäärää, mikä johtaa usein korkealaatuisiin kalvoihin.
Atomikerroksen laskeuma (ALD)
Atomikerroksen laskeuma muodostaa ohutkalvoja kerrosamalla vain muutamia atomikerroksia kerrallaan. Avain tähän menetelmään on kiertää riippumattomia vaiheita, jotka suoritetaan tietyssä järjestyksessä ja ylläpitää hyvää hallintaa. Kiekkopinnan päällyste esiasteella on ensimmäinen vaihe, ja sitten erilaiset kaasut otetaan reagoimaan edeltäjän kanssa halutun aineen muodostamiseksi kiekkojen pinnalle.
Fyysinen höyryn laskeuma (PVD)
Kuten nimestä voi viitata, fyysinen höyryn laskeutuminen viittaa ohuiden kalvojen muodostumiseen fyysisesti. Sputtering on fyysinen höyryn laskeutumismenetelmä, joka käyttää argon -plasmaa atomien ruiskuttamiseen kohteesta ja tallettaa ne kiekon pinnalle ohuen kalvon muodostamiseksi. Joissakin tapauksissa talletettua kalvoa voidaan hoitaa ja parantaa tekniikoilla, kuten ultraviolettilämpökäsittelyllä (UVTP).
Vaihe 6: Yhteydet
Puolijohteiden johtavuus on johtimien ja ei-johtajien (ts. Eristimien) välillä, mikä antaa meille mahdollisuuden hallita kokonaan sähkön virtausta. Kiekkopohjainen litografia, etsaus- ja kerrostumisprosessit voivat rakentaa komponentteja, kuten transistoreita, mutta ne on kytketty kytkemisen ja signaalien siirron ja vastaanottamisen mahdollistamiseksi.
Metalleja käytetään piirikiiteisiin niiden johtavuuden vuoksi. Puolijohteisiin käytettyjen metallien on täytettävä seuraavat ehdot:
· Matala resistiivisyys: Koska metallipiirien on läpäistävä virta, niiden metallien tulisi olla alhainen vastus.
· Lämpökemiallinen vakaus: Metallimateriaalien ominaisuuksien on pysyttävä muuttumattomina metallin yhdistämisprosessin aikana.
· Korkea luotettavuus: Kun integroitu piiritekniikka kehittyy, jopa pienillä määrillä metallialueiden välisiä materiaaleja on oltava riittävä kestävyys.
· Valmistuskustannukset: Vaikka kolme ensimmäistä ehtoa täyttyvät, aineelliset kustannukset ovat liian korkeat massatuotannon tarpeiden tyydyttämiseksi.
Yhdistämisprosessi käyttää pääasiassa kahta materiaalia, alumiinia ja kuparia.
Alumiinikytkentäprosessi
Alumiinikytkentäprosessi alkaa alumiinista laskeutumisella, fotoresistisella levityksellä, altistumisella ja kehityksellä, mitä seuraa etsaus ylimääräisen alumiinin ja fotorisistien poistamiseksi valikoivasti ennen hapetusprosessin syöttämistä. Kun yllä olevat vaiheet on suoritettu, fotolitografia, etsaus- ja laskeutumisprosessit toistetaan, kunnes yhteenliite on valmis.
Erinomaisen johtavuuden lisäksi alumiini on myös helppo fotolitografia, etsausta ja talletusta. Lisäksi sillä on edullinen ja hyvä tarttuvuus oksidikalvoon. Sen haitat ovat, että se on helppo syöpistää ja siinä on pieni sulamispiste. Lisäksi alumiinin reagoimisen estämiseksi piin kanssa ja aiheuttaen liitäntäongelmia, metallikerrokset on lisättävä erillisestä alumiinista kiekosta. Tätä talletusta kutsutaan "estemetalliksi".
Alumiinipiirit muodostetaan laskeutumisella. Kun kiekko tulee tyhjiökammioon, alumiinihiukkasten muodostama ohutkalvo tarttuu kiekkoon. Tätä prosessia kutsutaan "höyryn laskeutumiseen (VD)", joka sisältää kemiallisen höyryn laskeutumisen ja fysikaalisen höyryn laskeutumisen.
Kuparikyntäysprosessi
Kun puolijohdeprosessit muuttuvat hienostuneemmiksi ja laitekoot kutistuvat, alumiinipiireiden yhteydenopeus ja sähköiset ominaisuudet eivät ole enää riittäviä, ja tarvitaan uusia kapellimestareita, jotka täyttävät sekä koko- että kustannusvaatimukset. Ensimmäinen syy, miksi kupari voi korvata alumiinia, on, että sillä on alhaisempi vastus, mikä mahdollistaa nopeamman laitteen yhteydenopeuden. Kupari on myös luotettavampi, koska se on kestävämpi sähkömuutokselle, metalli -ionien liikkumiselle, kun virta virtaa metallin läpi kuin alumiini.
Kupari ei kuitenkaan muodosta helposti yhdisteitä, mikä vaikeuttaa höyrystää ja poistaa kiekon pinnasta. Tämän ongelman ratkaisemiseksi kuparin etsaamisen sijasta talletamme ja syövimme dielektrisiä materiaaleja, jotka muodostavat metallilinjakuvioita, jotka koostuvat kaivoksista ja viaista tarvittaessa, ja täytä sitten edellä mainitut "kuviot" kuparilla kytkentäen saavuttamiseksi, "damascene" -prosessi.
Kun kupariatomit edelleen diffuusi dielektriseen, jälkimmäisen eristys pienenee ja luo estekerroksen, joka estää kupariatomit lisää diffuusiosta. Sitten muodostetaan ohut kuparinsiemenkerros. Tämä vaihe sallii sähkösopulaation, joka on korkean kuvasuhteen kuvioiden täyttäminen kuparilla. Täyttämisen jälkeen ylimääräinen kupari voidaan poistaa metallikemiallisella mekaanisella kiillotuksella (CMP). Valmistumisen jälkeen oksidikalvo voidaan tallettaa, ja ylimääräinen kalvo voidaan poistaa fotolitografialla ja etsausprosesseilla. Yllä oleva prosessi on toistettava, kunnes kuparikytkentä on valmis.
Yllä olevasta vertailusta voidaan nähdä, että ero kuparikytkennän ja alumiinin yhdistämisen välillä on, että ylimääräinen kupari poistetaan metallisella CMP: llä etsaamalla.
Vaihe 7: Testaus
Testin päätavoitteena on tarkistaa, kohtaako puolijohdisirun laatu tiettyyn standardiin viallisten tuotteiden poistamiseksi ja sirun luotettavuuden parantamiseksi. Lisäksi testatut vialliset tuotteet eivät tule pakkausvaiheeseen, mikä auttaa säästämään kustannuksia ja aikaa. Elektroninen die -lajittelu (EDS) on testimenetelmä kiekoille.
EDS on prosessi, joka varmistaa kunkin sirun sähköominaisuudet kiekkotilassa ja parantaa siten puolijohdetuottoa. EDS voidaan jakaa viiteen vaiheeseen seuraavasti:
01 Sähköparametrin valvonta (EPM)
EPM on ensimmäinen askel puolijohdemurhien testissä. Tämä vaihe testaa jokaisen laitteen (mukaan lukien transistorit, kondensaattorit ja diodit), joita vaaditaan puolijohde -integroiduille piireille varmistaakseen, että niiden sähköparametrit täyttävät standardit. EPM: n päätehtävä on tarjota mitattu sähköinen ominaisuustieto, jota käytetään puolijohteiden valmistusprosessien ja tuotteiden suorituskyvyn tehokkuuden parantamiseksi (ei viallisten tuotteiden havaitsemiseksi).
02 Kiekkojen ikääntymistesti
Puolijohdevaurioiden määrä tulee kahdesta näkökulmasta, nimittäin valmistusvaurioiden nopeudesta (varhaisessa vaiheessa korkeampi) ja koko elinkaaren vikojen määrä. Kiekkojen ikääntymistesti viittaa kiekon testaamiseen tietyn lämpötilan ja AC/DC -jännitteen alla selvittääksesi tuotteet, joilla voi olla vikoja varhaisessa vaiheessa, toisin sanoen lopputuotteen luotettavuuden parantamiseksi löytämällä mahdolliset puutteet.
03 havaitseminen
Kun ikääntymistesti on suoritettu, puolijohdisiru on kytkettävä testilaitteeseen anturin kortilla, ja sitten kiekkolle voidaan suorittaa lämpötila, nopeus ja liikekokeet asiaankuuluvien puolijohdetoimintojen tarkistamiseksi. Katso taulukosta kuvaus tietyistä testivaiheista.
04 Korjaus
Korjaus on tärkein testivaihe, koska jotkut vialliset sirut voidaan korjata vaihtamalla ongelmalliset komponentit.
05 Dotting
Sähkötestin epäonnistuneet sirut on selvitetty edellisissä vaiheissa, mutta ne on silti merkitty niiden erottamiseksi. Aikaisemmin meidän piti merkitä viallisia siruja erityisellä musteella varmistaaksemme, että ne voidaan tunnistaa paljain silmällä, mutta nyt järjestelmä lajittelee ne automaattisesti testitietojen arvon mukaisesti.
Vaihe 8: Pakkaus
Edellisten useiden prosessien jälkeen kiekko muodostaa samankokoiset neliöpiirit (tunnetaan myös nimellä "yksittäiset sirut"). Seuraava tehtävä on saada yksittäiset sirut leikkaamalla. Äskettäin leikatut sirut ovat erittäin hauraita eivätkä pysty vaihtamaan sähköisiä signaaleja, joten ne on käsiteltävä erikseen. Tämä prosessi on pakkaus, joka sisältää suojakuoren muodostamisen puolijohdisirun ulkopuolelle ja antaa heille mahdollisuuden vaihtaa sähkösignaaleja ulkopuolelta. Koko pakkausprosessi on jaettu viiteen vaiheeseen, nimittäin kiekkojen sahaamiseen, yksisirun kiinnitys, yhteenliittäminen, muovaus- ja pakkaustestaus.
01 kiekon sahaus
Jotta voitaisiin leikata lukemattomia tiheästi järjestettyjä siruja kiekosta, meidän on ensin "jauhaa" kiekon takaosaa, kunnes sen paksuus vastaa pakkausprosessin tarpeita. Hiomisen jälkeen voimme leikata kiekon kirjoittajaviivaa pitkin, kunnes puolijohdepiiri on erotettu.
Konohkojen sahaustekniikkaa on kolme tyyppiä: terän leikkaus, laserleikkaus ja plasman leikkaus. Terän kuutiominen on timanttiterän käyttö kiekon leikkaamiseen, joka on alttiina kitkalämpölle ja roskille ja vahingoittaa siten kiekoa. Laserkuormituksella on suurempi tarkkuus, ja se pystyy helposti käsittelemään kiekkoja, joilla on ohut paksuus tai pieni kirjoituslinjaväli. Plasmakuormitus käyttää plasman etsauksen periaatetta, joten myös tätä tekniikkaa voidaan soveltaa, vaikka Scribe -linjaväli on hyvin pieni.
02 Yhden kiekon kiinnitys
Kun kaikki sirut on erotettu kiekosta, meidän on kiinnitettävä yksittäiset sirut (yksi kiekot) substraattiin (lyijykehys). Substraatin tehtävänä on suojata puolijohdisiruja ja antaa heille mahdollisuuden vaihtaa sähköisiä signaaleja ulkoisten piirien kanssa. Sirujen kiinnittämiseen voidaan käyttää nestemäisiä tai kiinteitä nauhoja.
03 Yhdistäminen
Kun siru on kiinnitetty substraattiin, meidän on myös kytkettävä näiden kahden kosketuspisteet sähköisen signaalinvaihdon saavuttamiseksi. Tässä vaiheessa voidaan käyttää kaksi liitäntämenetelmää: lankatodistus ohuilla metallilangoilla ja kääntö siru -sidoksella pallomaisten kultalohkojen tai tinalohkojen avulla. Lankimiitos on perinteinen menetelmä, ja kääntö siru -sidostekniikka voi nopeuttaa puolijohteiden valmistusta.
04 Muovaus
Puolijohdisirun kytkentä valmistumisen jälkeen tarvitaan muovausprosessi, joka lisää pakkauksen sirun ulkopuolelle puolijohde -integroidun piirin suojaamiseksi ulkoisilta olosuhteista, kuten lämpötila ja kosteus. Kun pakkausmuotti on valmistettu tarpeen mukaan, meidän on laitettava puolijohdepiiri ja epoksin muovausyhdiste (EMC) muottiin ja suljettava se. Suljettu siru on viimeinen lomake.
05 Pakkaustesti
Sirujen, joilla on jo ollut lopullinen muoto, on myös läpäistävä lopullinen vikatesti. Kaikki lopulliseen testiin tulevat valmiit puolijohdisirut ovat valmiita puolijohdepiireihin. Ne sijoitetaan testilaitteisiin ja asetetaan erilaisia olosuhteita, kuten jännite, lämpötila ja kosteus sähköisille, toiminnallisille ja nopeuskokeille. Näiden testien tuloksia voidaan käyttää vikojen löytämiseen ja tuotteiden laadun ja tuotannon tehokkuuden parantamiseen.
Pakkaustekniikan kehitys
Kun sirun koko pienenee ja suorituskykyvaatimukset kasvavat, pakkaukset ovat viime vuosina käyneet monia teknologisia innovaatioita. Joitakin tulevaisuuteen suuntautuneita pakkaustekniikoita ja ratkaisuja ovat kerrostumisen käyttö perinteisiin taustaprosesseihin, kuten kiekkojen tason pakkauksiin (WLP), räjähdysprosesseihin ja uudelleenjakelukerroksen (RDL) tekniikkaan sekä etsaus- ja puhdistustekniikkaan etuosan valmistukseen.
Mikä on edistynyt pakkaus?
Perinteinen pakkaus edellyttää, että jokainen siru leikataan kiekosta ja asetetaan muottiin. Kiekkojen tason pakkaus (WLP) on eräänlainen edistyksellinen pakkaustekniikka, joka viittaa sirun pakkaamiseen suoraan kiekkoon. WLP: n prosessi on pakata ja testata ensin ja erottaa sitten kaikki muodostetut sirut kiekosta kerralla. Perinteiseen pakkaukseen verrattuna WLP: n etu on alhaisemmat tuotantokustannukset.
Edistyneen pakkauksen voidaan jakaa 2D -pakkauksiin, 2,5D -pakkauksiin ja 3D -pakkauksiin.
Pienempi 2D -pakkaus
Kuten aikaisemmin mainittiin, pakkausprosessin päätarkoitus sisältää puolijohdisirun signaalin lähettämisen ulkopuolelle, ja kiekkoon muodostuneet kuopat ovat yhteyspisteitä syöttö-/lähtösignaalien lähettämiseen. Nämä kuopat on jaettu tuulettimeen ja tuulettimiin. Entinen tuulettimen muotoinen on sirun sisällä, ja jälkimmäinen tuulettimen muotoinen on sirualueen ulkopuolella. Kutsumme tulo-/lähtösignaaliksi I/O (tulo/lähtö), ja tulo/lähtösuunta on nimeltään I/O -luku. I/O -luku on tärkeä perusta pakkausmenetelmän määrittämiselle. Jos I/O-luku on alhainen, käytetään tuulettimen pakkausta. Koska sirun koko ei muutu paljon pakkaamisen jälkeen, tätä prosessia kutsutaan myös siru-asteikon pakkaukseksi (CSP) tai kiekkotason siru-mittakaavapakkauksiksi (WLCSP). Jos I/O-lukumäärä on korkea, tuulettimien pakkauksia käytetään yleensä ja uudelleenjakelukerroksia (RDL) tarvitaan kuoppien lisäksi signaalin reitityksen mahdollistamiseksi. Tämä on "Fan-Out-kiekkotason pakkaus (Fowlp)".
2.5D -pakkaus
2.5D -pakkaustekniikka voi laittaa kaksi tai useampia sirutyyppejä yhdeksi pakkaukseksi samalla kun signaalit voidaan ohjata sivusuunnassa, mikä voi lisätä paketin kokoa ja suorituskykyä. Yleisimmin käytetty 2.5D -pakkausmenetelmä on laittaa muisti- ja logiikkalastuja yhdeksi pakkaukseksi piinvälisen interposerin kautta. 2.5D-pakkaus vaatii ydinteknologioita, kuten yli-liikoni ViaS (TSV), mikrohoput ja hienovarainen RDLS.
3D -pakkaus
3D -pakkaustekniikka voi laittaa kaksi tai useampia sirutyyppejä yhdeksi pakkaukseksi samalla kun signaalit voidaan reitittää pystysuunnassa. Tämä tekniikka soveltuu pienemmille ja korkeammalle I/O -laskenta -puolijohdisiruille. TSV: tä voidaan käyttää siruihin, joilla on korkea I/O -lukumäärä, ja lankatodistusta voidaan käyttää siruihin, joilla on alhaiset I/O -määrät, ja lopulta muodostavat signaalijärjestelmän, johon sirut on järjestetty pystysuunnassa. 3D-pakkaukseen tarvittavat ydinteknologiat sisältävät TSV: n ja mikro-bump-tekniikan.
Toistaiseksi puolijohdetuotteiden valmistuksen kahdeksan askelta "Konekonprosessointi - hapettuminen - fotolitografia - etsaus - ohutkalvojen laskeuma - yhdistäminen - testaus - pakkaus" on otettu kokonaan käyttöön. Semiconductor Technology suorittaa "hiekasta" "siruihin", jotka suorittavat todellisen version "Kiven kääntämisestä kultaksi".
Vetek Semiconductor on ammattimainen kiinalainen valmistajaTantaalikarbidipinnoite, Piikarbidipinnoite, Erityinen grafiitti, PiiharbidikeramiikkajaMuu puolijohdekeramiikka. Vetek Semiconductor on sitoutunut tarjoamaan edistyneitä ratkaisuja erilaisille sic -kiekkotuotteille puolijohdeteollisuudelle.
Jos olet kiinnostunut yllä olevista tuotteista, ota rohkeasti yhteyttä suoraan.
MOB: +86-180 6922 0752
Whatsapp: +86 180 6922 0752
Sähköposti: anny@veteemiemi.com
+86-579-87223657
Wangda Road, Ziyang Street, Wuyi County, Jinhua City, Zhejiangin maakunta, Kiina
Copyright © 2024 Veek Semiconductor Technology Co., Ltd. Kaikki oikeudet pidätetään.
Links | Sitemap | RSS | XML | Privacy Policy |